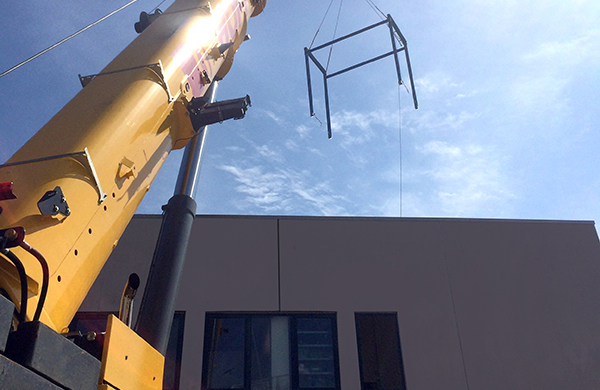
Factory 2 in Cloppenburg
Investments Worth € 8.5 Million are Manifesting
The largest production site of the Lumberg Group located in Lower-Saxony’s Cloppenburg will be given a total facelift. It is here that Lumberg will once again strengthen its Automotive business segment with a crucial component for an oil pump motor with integrated electronics, which creates the necessary pressure in a motorcar transmission. A production that meets cleanroom conditions is what is needed. These building measures and the investments for this automotive project boost Lumberg’s position as a proficient system supplier of mechatronic units especially for Tier 1 automotive suppliers.
It was quite a spectacular sight when the low-loader recently drove onto the grounds on Alten Emsteker Weg in Cloppenburg: The injection molding machine from the Selecta model range of the world’s leading manufacturer, Arburg based in Loßburg in the Black Forest, with its components painted in typically vibrant hues of green and yellow and measuring roughly 6 meters in length, 5 meters in height and 2.5 meters in width, was positioned by a crane on several air cushions. The crane had to lift a good 19 tons in weight, which, once floating on a thin layer of air of 0.01 mm, had to be maneuvered to the right spot inside the large factory.
Equally spectacular were the actual preparations inside the factory hall: Arburg’s machine, which Lumberg has been relying on for decades for the serial production of its plastic parts, exceeds the physical roof of the hall because of the vertical injection unit’s solid height of roughly 5 meters. Hall I was converted and given a glass dome and it is exactly here that Arburg’s vertical all-round talent has to be set up. This part of the hall will also be expanded to accommodate a so-called cleanroom, i.e. it will cater to the production of clean-sensitive sub-assemblies for which special controls apply to prevent or minimize particles from the outside, the spread of particles and the creation of particles during the actual process. In addition to special paint on the walls and floors, the closed area will only be accessible to specific employees via a sluice.
In a second step, a central ventilation unit featuring a heat recovery system with a plate heat exchanger and a volume flow capacity of 13,400 m³/h was installed on the hall’s roof. The unit is over 13 meters long and weighs 6 tons. 2 air hoses source the air intake and direct it into the cleanroom while the outgoing air is centrally suctioned off at the ceiling. Two air-cooled ONI cooling units, with a cooling capacity of 80 and 62 kW respectively and weighing 1.37 t and 960 kg, are also part of the system.
In a final step Arburg installs a two-strand Abus overhead crane with a 6.8 m span and a carrying capacity of 1.6 tons.
Overall, these machines, the conversion measures for the machine, the necessary punching and injection tools and assembly lines – which Lumberg developed and built at the in-house tool manufacturing in Cloppenburg and Schalksmühle – and the required peripherals from the furnace via special ventilation and measuring systems – consumed a good 4.5 million euros for this hall alone. With this step, Lumberg will once again strengthen its Automotive business segment with a crucial component for an oil pump motor with integrated electronics, which creates the necessary pressure in a motorcar transmission. These building measures and investments for this automotive project boost Lumberg’s position as a proficient system supplier of mechatronic units especially for Tier 1 automotive suppliers.
Media Contact:
Lumberg Holding GmbH & Co. KG
Im Gewerbepark 2
58579 Schalksmühle
Germany
Kai Rotthaus
T +49 2355 83-1275
Article as PDF